Healthcare Storage Solutions
Storage Solutions for the Healthcare Supply Chain
Like many businesses today, healthcare service facilities including medical labs, diagnostic labs, home healthcare services, dialysis centers and specialty outpatient facilities are striving to provide the best services at the lowest cost. We at V&H Material Handling have the experience to apply the proper automation to reduce costs while providing superior services to the hospital and the departments within the hospital.
Products for Hospital Logistics and Healthcare Services
Benefits of Our Healthcare Storage Solutions
Part Traceability
Complete traceability is no easy task. Inventory management software provides real time information for traceability, can reduce stock levels and can generate on demand reports with little effort.
Labor Efficiencies
All Kardex technology is designed to bring items to the person, eliminating walk and search time commonly associated with drawers and shelving. This creates a labor savings opportunity and makes efficient use of the facilities floor space and cube.
Increased Storage
Kardex automated storage and retrieval systems can save up to 85 % of floor space. This allows facilities to utilize this additional floor space for other value-added activities.
Improved Order Picking
All Kardex technology is designed to bring items to the worker, eliminating walk and search time, increasing productivity. This helps get orders out the door on time.
Leaning Out Waste
Very often hospitals are using outdated technology and antiquated processes in their materials handling flow. By implementing dynamic storage and retrieval solutions such as horizontal and vertical carousels to increase pick accuracy, improve productivity and save space: hospitals are leaning out wasted time and money in current processes. By implementing these systems, hospitals have realized sustainable reductions of waste attributable to labor, inflated inventories, expired product costs, lost items and workplace injury.
Our solutions are designed to be modular and can be integrated in stages into any workflow, regardless of its current level of automation.
Children's Hospital Center Pictures
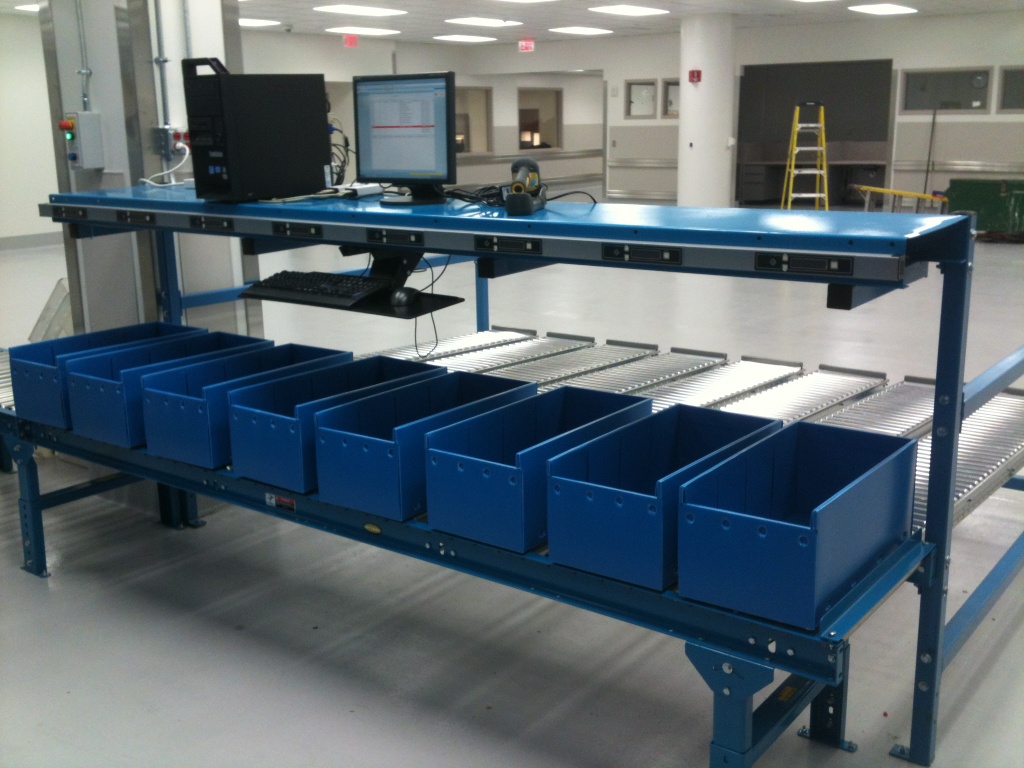
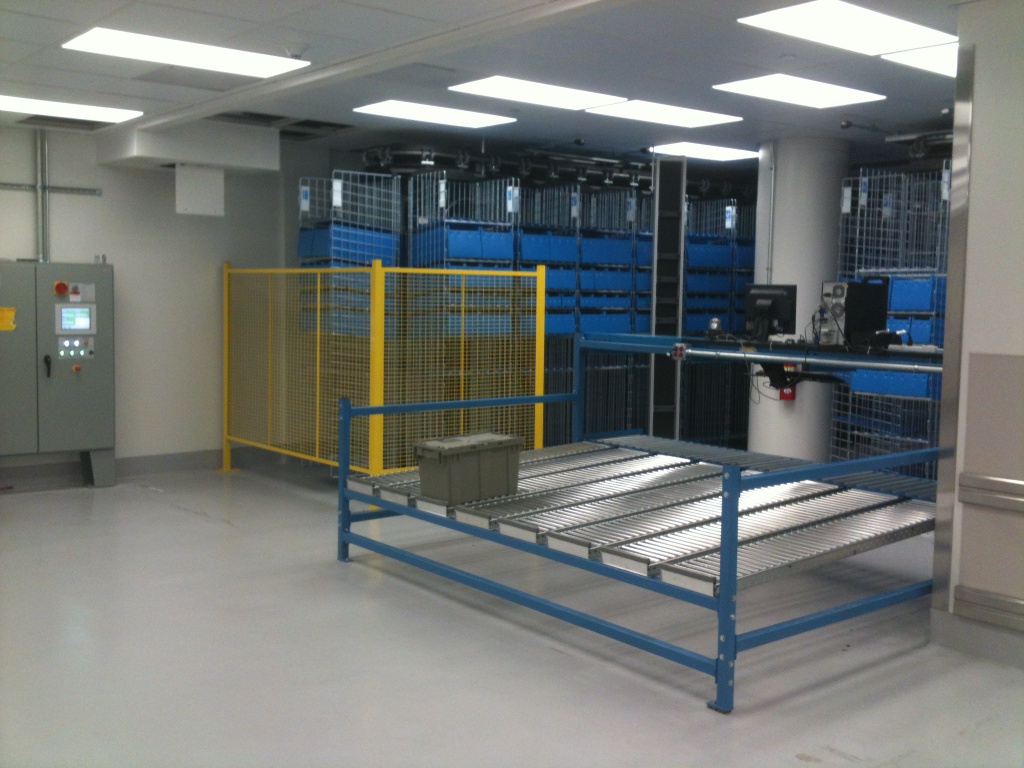
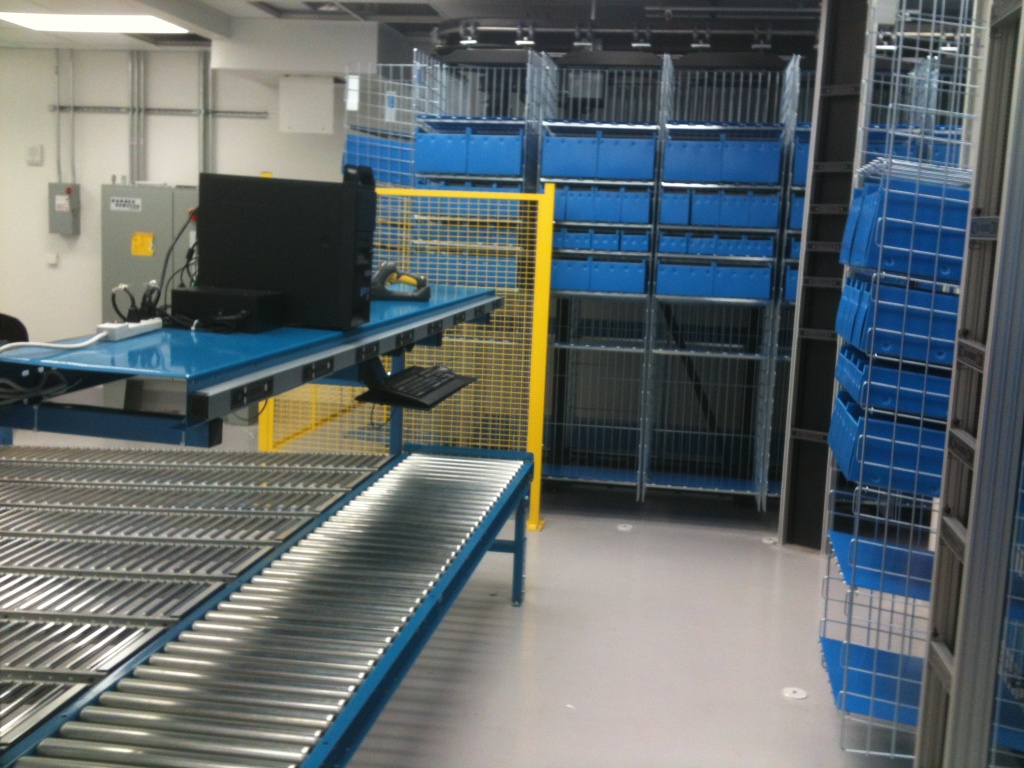
Additional Storage Solutions Offered
High Density Secure Pathology Slide/Tissue Block Storage
Medical laboratories and hospitals are mandated to keep pathology slides and tissue blocks for a specific timeframe. Although retention periods vary based on specimen type, some can be up to ten years. Storing pathology slides and tissue blocks for ten years comes with a unique set of challenges including storage space, weight limitations, confidentiality and tracking/retrieving. The Kardex Remstar Pathology Unit is specially designed to meet these unique challenges providing high density, secure storage and retrieval for pathology slides and tissue blocks. Units can be dedicated for pathology slides and tissue blocks or mixed and matched to meet active laboratories daily needs, keeping items at your fingertips.
Benefits:
- Save Up To 75% Floor Space
- 100% Ergonomic Accessibility
- Improve Slide Security
- Increase Productivity
- Virtually Eliminate Damage from Slide Mishandling
Operations:
The Pathology Unit is designed to support the weight of the slide and tissue blocks inventory (0.28 lbs./LFI) while increasing slide density. Laboratories can save up to 75% floor space using the Pathology Unit over other standard pathology slide and tissue blocks storage methods.
Case Studies for Healthcare Storage Solutions
Case study #1
Case study #2
SITE
Wausau Hospital
Wausau, WI
APPLICATION
Distribution of med-surgical supplies to the hospital
EQUIPMENT
Four horizontal carousels, Pick Light Towers and FastPic® software
SUMMARY
One horizontal workstation has reduced floor space 75% while increasing accuracy to 100% and reducing the cost per pick by 88%
SITE
Mazak
Florence, Kentucky
APPLICATION
Parts distribution to end users
EQUIPMENT
13 Shuttle® VLMs grouped in four pick-and-pass workstations integrated with FastPic® Inventory Management Software
SUMMARY
Improved productivity by 80% while reducing labor requirements by 44% and increased part numbers by 95%